Heutzutage spielen Windkraftanlagen eine wesentliche Rolle bei der Erzeugung erneuerbarer Energie, um dem vieldiskutierten Thema des globalen Klimawandels entgegenzuwirken. Obwohl sie einfach aussehen, sind Windkraftanlagen hochkomplexe und große technische Systeme, deren Instandhaltung eine Herausforderung darstellt. Eine sorgfältige Wartung ist jedoch entscheidend, da Fehlentscheidungen schwerwiegende Folgen haben können. Daher ist die Entwicklung einer Strategie notwendig, die im Idealfall optimale Wartungsentscheidungen sicherstellt.
Wir leben in einer Ära wachsenden Umweltbewusstseins. Dazu gehört die Erzeugung erneuerbarer Energien, bei der Windkraftanlagen eine zentrale Rolle spielen. Sie wandeln die kinetische Energie des Windes in elektrische Energie um und tragen so maßgeblich zur Reduzierung von Kohlendioxidemissionen bei. Ein weiterer Vorteil ist, dass Windenergie unerschöpflich ist, was uns unabhängiger von anderen Energieressourcen macht. Windkraftanlagen sind jedoch gigantische Maschinen, deren Wartung sich entsprechend schwierig gestalten kann.
Planmäßige Wartung
Ursprünglich wurden Wartungsarbeiten nach einem vordefinierten Zeitplan durchgeführt, was als “planmäßige Wartung” bezeichnet wird. Ziel der planmäßigen Wartung ist es, die Ausfallzeiten der Windkraftanlage zu reduzieren, indem alle notwendigen Ressourcen und Ersatzteile vor Ort sind und eine spezifische Strategie für deren Einsatz verfolgt wird. Diese Art der Wartung ist jedoch alles andere als optimal. Im Idealfall möchten wir eine Wartung genau dann durchführen, kurz bevor an der Anlage ein Schaden entsteht. Eine vorzeitige Wartung, d.h. eine Wartung, die einige Zeit vor dem Eintreten eines Problems durchgeführt wird, führt zu unnötigen Ausfallzeiten. Andererseits führt eine verspätete Wartung, d.h. eine Wartung, die erst einige Zeit nach dem Auftreten eines kritischen Problems angesetzt wird, zu einem Ausfall, der hätte vermieden werden können. Hohe Reparaturkosten und lange Lieferzeiten für teure Ersatzteile, die aufgrund unvorhergesehener Umstände erst bestellt werden müssen, führen zusätzlich zu weiteren Kosten und längeren Stillstandszeiten.
Zeit ist Geld
Es gibt jedoch ein weiteres Problem bei diesem Wartungsansatz, das leicht übersehen wird: Die planmäßige Wartung berücksichtigt nicht die Ausbreitung eines Fehlers. So können sich beispielsweise winzige Risse in einem Rotorblatt, die durch einen Blitzeinschlag entstanden sind, mit der Zeit vergrößern und schließlich zu einem fatalen Schaden im Getriebe führen. Zu Beginn sind die Risse so klein, dass sie bei einer regulären Inspektion wahrscheinlich unbemerkt bleiben. Bei einer späteren Inspektion werden die Risse vielleicht bemerkt, aber dann ist es höchstwahrscheinlich bereits zu spät.
Um das Ausmaß des Problems zu verdeutlichen: Der Austausch allein des Getriebes kann über 230.000 US-Dollar kosten, und die Reparaturzeit kann sich leicht über eine ganze Woche erstrecken (Carroll, McDonald, & McMillan, 2016). Man beachte, dass dies nur die reine Reparaturzeit umfasst und keine Zeiten wie Anreise, Vorlaufzeiten oder Verzögerungen durch schwere Erreichbarkeit berücksichtigt, sodass die tatsächliche Ausfallzeit i.d.R. noch länger ist. Während der Ausfallzeit ist die Windkraftanlage überhaupt nicht profitabel; in diesem Fall bedeutet Zeit also buchstäblich Geld. Diese planmäßige Wartungsstrategie in Verbindung mit einem ungünstigen Zeitpunkt des Ausfalls hat somit enorme Konsequenzen, insbesondere in finanzieller Hinsicht. Die natürliche Frage, die sich stellt, lautet: Wie können wir unsere Wartungsstrategie verbessern, um den finanziellen Schaden im Falle eines bevorstehenden Ausfalls der Windkraftanlage zu minimieren?
Zustandsorientierte Instandhaltung
Hier setzt das Konzept der zustandsorientierten Instandhaltung an. Wie der Name schon sagt, ist die zustandsorientierte Instandhaltung eine Strategie, die den tatsächlichen Zustand der Windkraftanlage überwacht, um zu entscheiden, wann und welche Wartungsarbeiten durchgeführt werden müssen. Zu diesem Zweck sind Windkraftanlagen heute mit fortschrittlichen Sensoren ausgestattet, die Variablen wie Temperaturen, Vibrationen und Leistungsabgabe messen können. Auf diese Weise verfügen wir über genügend Echtzeit-Sensordaten, um den Zustand mehrerer Komponenten im Betrieb zu verfolgen und somit den Gesamtzustand der Windkraftanlage zu überwachen.
Mithilfe eines geeigneten statistischen Rahmenwerks, das der Methodik der Statistischen Prozesskontrolle folgt, können wir eine zuverlässige Regelkarte erstellen. Diese enthält für jeden Zeitpunkt eine Teststatistik, entsprechende Eingriffsgrenzen und ein Warnsignal, wenn die Teststatistik eine dieser Grenzen über- oder unterschreitet. Ein solches Warnsignal deutet auf eine Out-of-Control-Situation hin, die ein Problem innerhalb der Windkraftanlage anzeigen könnte. Solche Regelkarten ermöglichen es uns, (kleine) Abweichungen vom normalen Verhalten, die auf einen bevorstehenden Ausfall hindeuten könnten, präzise und zeitnah zu erkennen. Diese Abweichungen sollten anschließend auf die ursprüngliche Fehlerursache zurückverfolgt werden, auf deren Grundlage dann angemessene Wartungsentscheidungen getroffen werden können. Diese Strategie gewährleistet optimale Wartungsintervalle, da die Wartung nur dann durchgeführt wird, wenn sie wirklich notwendig ist. Indem alle erforderlichen Ressourcen rechtzeitig bereitgestellt werden, wird zudem der Zeitaufwand für die Wartung minimiert. Und nicht zuletzt minimiert die schnelle und zuverlässige Erkennung nachlassender Leistung Gemeinkosten und Ausfallzeiten aufgrund unerwarteter Ausfälle.
Ein Beispiel aus der Praxis
Wir werden die Vorteile der zustandsorientierten Instandhaltung anhand eines realen Beispiels veranschaulichen, bei dem wir Daten einer Windkraftanlage verwenden, die von einem niederländischen Energieversorger zur Verfügung gestellt wurden. Die Sensordaten wurden über einen Zeitraum von fast zwei Jahren erfasst und umfassen 229.680 Beobachtungen für 110 Variablen, die alle vier Minuten gemessen wurden. Die wichtigsten Variablen lassen sich in zwei Kategorien unterteilen:
- Umgebungsvariablen: Variablen, die Umweltfaktoren wie Windgeschwindigkeit und Umgebungstemperatur beschreiben.
- Zustandsvariablen: Variablen, die den Zustand verschiedener Komponenten der Windkraftanlage beschreiben. Diese lassen sich weiter unterteilen in:
- Drehzahl: Rotordrehzahl (rotor speed) und Generatordrehzahl (generator speed).
- Temperaturen: Messungen der Lager- (bearing), Getriebe- (gearbox), Hauptgenerator- (main generator), Startgenerator- (starting generator), Gondel- (nacelle) und Öltemperaturen (oil temperatures).
- Vibrationen: Verschiedene Schwingungsmessungen an diversen Komponenten.
- Betriebsdaten: Leistungsabgabe, Betriebszustand, Anstellwinkel (pitch angle) und Gier-Messungen (yaw measurements).
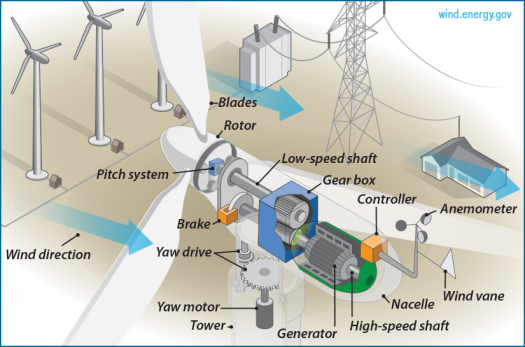
Um ein besseres Verständnis für das Innere einer Windkraftanlage zu bekommen, sind die meisten der zugehörigen Komponenten in Abbildung 1 dargestellt.
Wir wissen, dass die Windkraftanlage kürzlich einen mechanischen Defekt am Hauptgenerator erlitten hat. Obwohl das Problem bereits vermutet wurde, wurden die eigentliche Ursache und das Ausmaß des Schadens erst bei der Inspektion nach dem Ausfall deutlich. Hätten wir anstelle einer planmäßigen Wartungsstrategie eine zustandsorientierte Instandhaltungsstrategie verfolgt, hätten wir die folgende Regelkarte erhalten:
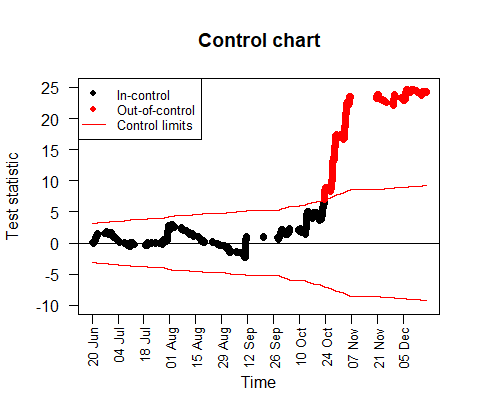
Aus dieser Regelkarte können wir schließen, dass Mitte Oktober erste ernsthafte Warnungen auftraten, die auf eine problematische Situation innerhalb der Windkraftanlage hindeuteten. Bemerkenswert ist, dass diese Warnsignale etwa dreizehn Monate vor dem Ausfall des Hauptgenerators auftraten. Wenn wir annehmen, dass wir zu diesem Zeitpunkt die Fehlerursache korrekt hätten identifizieren können, hätten wir eine ordnungsgemäße Wartung durchführen und so den Ausfall des Hauptgenerators verhindern können. Auf diese Weise hätten wir eine enorme Geldsumme sparen können, indem wir nur etwa 3.500 US-Dollar für Reparaturkosten statt etwa 60.000 US-Dollar für die Austauschkosten des Hauptgenerators hätten zahlen müssen. Zusätzlich hätten wir die Gesamtausfallzeit um mindestens 57 Stunden reduzieren können (Carroll et al., 2016). Dieses spezielle Beispiel unterstreicht die Notwendigkeit der zustandsorientierten Instandhaltung, da die Vorteile – sowohl in Bezug auf Geld als auch auf Zeit – erheblich sind.
Haben Sie eine eigene Anwendung für Predictive Maintenance im Sinn?
Infobox:
Statistische Prozesskontrolle (engl. Statistical Process Control, SPC): Die Statistische Prozesskontrolle ist eine Methode der Qualitätskontrolle, die statistische Techniken zur Überwachung und Steuerung eines Prozesses einsetzt.
Referenzen:
- Carroll, J., McDonald, A., & McMillan, D. (2016). Failure rate, repair time and unscheduled O&M cost analysis of offshore wind turbines. Wind Energy, 19(6), 1107-1119.